Or try one of the following: 詹姆斯.com, adult swim, Afterdawn, Ajaxian, Andy Budd, Ask a Ninja, AtomEnabled.org, BBC News, BBC Arabic, BBC China, BBC Russia, Brent Simmons, Channel Frederator, CNN, Digg, Diggnation, Flickr, Google News, Google Video, Harvard Law, Hebrew Language, InfoWorld, iTunes, Japanese Language, Korean Language, mir.aculo.us, Movie Trailers, Newspond, Nick Bradbury, OK/Cancel, OS News, Phil Ringnalda, Photoshop Videocast, reddit, Romanian Language, Russian Language, Ryan Parman, Traditional Chinese Language, Technorati, Tim Bray, TUAW, TVgasm, UNEASYsilence, Web 2.0 Show, Windows Vista Blog, XKCD, Yahoo! News, You Tube, Zeldman
apt 123
apt 123What is Plastic Fabrication? 23 Jan 2025, 9:36 am
Plastic fabrication is the process of designing, manufacturing, and assembling plastic products through various methods. Unlike traditional metalworking, plastic fabrication involves working with different types of plastics, including thermoplastics, thermosets, and composites, to create durable and functional items for a wide range of industries. Whether it’s for creating everyday consumer products, specialised components for engineering, or large-scale installations, plastic fabrication offers numerous advantages, including lightweight, cost-effective, and versatile solutions.
How to Fabricate Plastic
Plastic fabrication encompasses several techniques, each chosen depending on the project’s requirements, such as the type of plastic, desired finish, complexity, and volume. Here are the main methods involved in fabricating plastic:
- Cutting and Slicing
The first step in many plastic fabrication projects involves cutting the material into the desired shape and size. Common methods include using saws, lasers, or water jets. For example, a circular saw can be used for straight cuts, while a laser cutter offers precision for intricate designs. Water jet cutting, often used for thicker plastics, provides clean, smooth edges with minimal material distortion. - Drilling and Boring
Drilling holes into plastic is a crucial step when creating parts that require fasteners, pipes, or ventilation. Plastics are generally easier to drill than metals, but the right type of drill bit must be used to prevent cracking. For larger, deeper holes, boring techniques are applied, especially when precision is important for fitting. - Thermoforming
Thermoforming involves heating a plastic sheet until it becomes soft and pliable, then moulding it into the desired shape using a mould. This technique is often used for creating large, shallow parts, such as trays, panels, and containers. The heated plastic sheet is vacuum-formed over a mould to create the desired shape, after which it is cooled and trimmed. - Injection Moulding
Injection moulding is a widely used plastic fabrication technique where molten plastic is injected into a mould cavity under high pressure. It’s an excellent method for producing large volumes of identical parts with intricate designs. Though it requires significant upfront investment in mould design and construction, it’s highly cost-effective for mass production. - Welding and Bonding
Plastic welding is the process of joining two plastic parts together by applying heat and pressure. There are different types of plastic welding, including hot air welding, ultrasonic welding, and vibration welding, each suited for different materials and applications. In addition to welding, bonding agents like adhesives and solvent-based glues can be used to join plastic pieces, offering a more flexible solution when welding isn’t viable. - Bending and Forming
Some plastic fabrication projects require bending or shaping the plastic to achieve curves or angles. Techniques like heat bending, where a plastic sheet is heated and then bent into shape, are common for creating angled parts or frames. In some cases, a mould or jig may be used to ensure consistent results. - Polishing and Finishing
After the plastic parts have been cut, drilled, or moulded, finishing touches are often required. Polishing the surface of the plastic enhances its appearance, removes any scratches or marks, and can make it more transparent or reflective. Other finishing processes, such as painting, coating, or texturing, can be applied to improve the plastic’s functionality or aesthetics.
Key Benefits of Plastic Fabrication
1. Versatility
Plastic fabrication can be used to create a vast array of products, ranging from simple plastic enclosures and signs to complex mechanical parts, custom prototypes, or architectural components. The variety of plastics available allows for tailored solutions for different needs, whether it’s lightweight, impact-resistant, or temperature-stable plastic that’s required.
2. Lightweight and Durable
One of the key advantages of plastic over materials like metal or wood is its lightweight nature. Plastics are often less dense, making products easier to transport and handle. Despite their light weight, plastics can be incredibly strong, durable, and resistant to wear, corrosion, and environmental conditions, making them ideal for a range of applications, from consumer goods to heavy-duty industrial parts.
3. Cost-Effectiveness
Compared to metals and other traditional materials, plastic fabrication tends to be more cost-effective. The materials themselves are typically less expensive, and many fabrication techniques (such as thermoforming or injection moulding) allow for high-volume production with minimal waste. The ability to produce intricate designs quickly and efficiently contributes to the affordability of plastic parts.
4. Customisation
Plastic fabrication offers significant flexibility in terms of customisation. From choosing the exact type of plastic to designing a part with specific dimensions, colours, and finishes, the process allows manufacturers to meet exact requirements. Whether it’s a one-off prototype or a mass-produced item, plastic fabrication provides a high degree of design freedom.
5. Sustainability
While some plastics have been criticised for their environmental impact, the rise of recyclable and biodegradable plastics has made the process more sustainable. Recycled plastic can be reused in many fabrication methods, reducing material waste. Additionally, many plastic products are designed to be durable and long-lasting, which can reduce the need for replacements and contribute to sustainability over time.
Applications of Plastic Fabrication
Plastic fabrication is used across a variety of industries, thanks to the material’s versatility. Here are some common examples:
- Construction: In construction, plastics are used for piping, insulation, roofing, and even interior finishes. Their lightweight nature and resistance to corrosion make them ideal for long-lasting installations.
- Automotive: The automotive industry uses plastic fabrication for producing a wide range of parts, from interior components like dashboards and panels to exterior elements like bumpers and trims. Plastic’s ability to reduce weight while maintaining strength helps improve vehicle fuel efficiency.
- Consumer Products: Everyday products such as containers, electronics casings, and kitchenware are often made through plastic fabrication. The ability to create complex shapes and customise colours makes plastic ideal for the consumer market.
- Medical Devices: The medical field uses plastic fabrication for producing medical equipment, from surgical tools to prosthetics and patient monitoring devices. The hygiene and durability of plastics make them particularly well-suited for medical applications.
- Signage and Displays: Fabricated plastic is widely used in signage, display units, and exhibition stands. The material can be moulded into intricate shapes and can be easily printed on, making it ideal for custom signs and promotional materials.
Conclusion
Plastic fabrication is an essential part of modern manufacturing, offering flexibility, cost-effectiveness, and design freedom across a wide range of industries. Whether you’re creating everyday consumer products, industrial components, or high-performance parts for specific applications, plastic fabrication can provide the solution. The diverse range of fabrication techniques available ensures that plastic can be moulded, cut, shaped, and assembled into virtually any form required, making it a go-to material for many sectors.
The post What is Plastic Fabrication? appeared first on apt 123.
What is Vacuum Forming? 23 Jan 2025, 9:27 am
Vacuum forming is a type of plastic moulding process that is used to create a wide variety of products, from packaging materials to automotive parts and even custom prototypes. As the name suggests, the process involves using vacuum pressure to shape a sheet of plastic over a mould. This relatively simple yet versatile technique has been around for decades and is widely utilised in various industries due to its speed, cost-effectiveness, and ability to produce detailed and lightweight products.
How Does Vacuum Forming Work?
The vacuum forming process begins with a flat sheet of plastic, usually made from materials such as ABS (Acrylonitrile Butadiene Styrene), PET (Polyethylene Terephthalate), or PVC (Polyvinyl Chloride). Here’s a step-by-step breakdown of how the process works:
- Heating the Plastic Sheet
The first step involves heating the plastic sheet to a temperature where it becomes soft and pliable. The sheet is typically heated using an oven or other specialised heating equipment. It needs to reach a temperature where it can easily stretch without breaking, but not so hot that it melts. - Positioning the Heated Sheet
Once the plastic has reached the right temperature, it is quickly moved to a vacuum forming machine. The sheet is placed over a mould (which could be made from materials like metal, wood, or composite material). The mould has the shape that you want to form the plastic into. - Applying the Vacuum
The most crucial part of the process comes next—vacuum pressure. A vacuum is applied under the plastic sheet, pulling it tightly against the contours of the mould. As the air is sucked out, the plastic begins to cling to the mould’s surface, conforming to its shape. This step happens rapidly to prevent the plastic from cooling prematurely. - Cooling and Solidifying
Once the plastic is stretched and clinging to the mould, it begins to cool and harden. The cooling time depends on the thickness of the plastic and the complexity of the mould. Cooling is critical because it allows the plastic to retain the exact shape of the mould once it hardens. - Removal and Finishing
After the plastic has cooled, it’s carefully removed from the mould. At this point, the formed plastic part may require additional finishing touches. Trimming excess plastic, drilling holes, painting, or adding any necessary hardware are common steps in preparing the part for its final use.
Key Benefits of Vacuum Forming
1. Cost-Effective Production
One of the primary reasons vacuum forming is so popular is its cost-effectiveness. The process is relatively simple compared to other moulding techniques, such as injection moulding or blow moulding. The moulds used in vacuum forming are typically less expensive to create, which makes it an ideal option for small to medium production runs. In fact, vacuum forming is often the go-to choice for prototyping or testing product designs before committing to larger-scale manufacturing processes.
2. Quick Turnaround Time
Because the process doesn’t require complex machinery or long setup times, vacuum forming allows for rapid production. This is especially beneficial when speed is a priority, whether for creating custom packaging, product prototypes, or small batches of a particular part. The simplicity of the process also reduces the likelihood of errors, further contributing to a fast turnaround.
3. Design Flexibility
Vacuum forming can produce parts with intricate details, especially when the mould is well-designed. The ability to form plastic over complex contours allows manufacturers to create aesthetically pleasing and functional products, from smooth, uniform shapes to parts with textured surfaces. Additionally, the moulds themselves can be modified or adjusted relatively easily, allowing for quick design iterations.
4. Lightweight and Durable Products
The products created through vacuum forming tend to be lightweight yet durable. The plastic sheets used in the process can be chosen for their strength, resistance to impact, and flexibility, making vacuum-formed products suitable for a wide range of applications. This is why vacuum forming is commonly used in the automotive industry, for creating interior panels, dashboards, and other lightweight components.
Applications of Vacuum Forming
The versatility of vacuum forming makes it suitable for a broad range of industries and applications. Here are some common examples:
- Packaging: Vacuum forming is widely used for creating packaging materials, such as clamshell packages, blister packs, and trays. These products help protect delicate items during shipping and offer an attractive way to display merchandise.
- Automotive Industry: Many automotive manufacturers use vacuum forming to produce lightweight interior components such as door panels, dashboards, and consoles. Vacuum forming allows for the creation of durable, yet lightweight parts that help reduce the overall weight of the vehicle.
- Consumer Products: Many household items, from plastic containers to electronic housings, are made using vacuum forming. The process is often used for producing high-volume products at a low cost.
- Medical Equipment: In the medical field, vacuum forming is used to create custom moulds and trays, such as those used for surgical instruments or for forming protective covers for medical devices.
- Prototyping: When designers need a physical model of a product or component, vacuum forming provides a quick and affordable way to create a prototype. It allows designers to test fit and form before committing to a more expensive manufacturing process.
Conclusion
Vacuum forming is a versatile and efficient process that has a wide range of applications across different industries. Its ability to produce lightweight, durable, and cost-effective products with minimal setup time makes it an attractive choice for manufacturers. Whether it’s for packaging, automotive parts, or prototypes, vacuum forming provides a solution that balances speed, flexibility, and cost efficiency.
The post What is Vacuum Forming? appeared first on apt 123.
Precision in Polymers 11 Jan 2024, 10:13 am
Precision in Polymers – Unveiling the Artistry of Laser Cutting and Engraving in the UK Manufacturing Sector:
Uncover the art of precision in polymers at APT. In the dynamic landscape of the UK manufacturing sector, one technology has emerged as a game-changer, offering unparalleled precision and versatility – laser cutting and engraving on plastics. This transformative process has redefined the way manufacturers approach plastic fabrication, unlocking a realm of possibilities in terms of design, functionality, and customisation. In this blog, we will delve into the types of plastics commonly used, the diverse applications of laser cutting and engraving, and the stunning finishes that can be achieved.
Types of Plastics:
Acrylic (PMMA):
Known for its transparency and optical clarity, acrylic is a popular choice for laser cutting and engraving. It allows for intricate designs and can be manipulated to create various finishes, from frosted to high gloss.
Polyethylene (PE) and Polypropylene (PP):
These thermoplastics are widely used in industries due to their durability and chemical resistance. Laser cutting on these plastics results in clean edges, making them suitable for applications like packaging, signage, and industrial components
Polycarbonate (PC):
Recognised for its impact resistance and optical properties, polycarbonate is often used in the production of electronic components and automotive parts. Laser cutting enables precision in shaping intricate details.
Polyvinyl Chloride (PVC):
PVC is a versatile plastic that finds applications in construction, signage, and even fashion. Laser engraving on PVC can produce aesthetically pleasing textures and patterns, while laser cutting ensures accuracy in shaping.
Applications of Laser Cutting and Engraving:
Signage and Displays:
Laser-cut and engraved acrylic and PVC are extensively employed in the creation of eye-catching signs and displays. The technology allows for intricate lettering and logos, enhancing brand visibility.
Prototyping and Production:
Laser cutting enables rapid prototyping by swiftly transforming digital designs into physical prototypes. Additionally, it is utilised in mass production for creating precise components with consistent quality.
Personalised Products:
From bespoke gifts to custom-designed electronic device casings, laser cutting and engraving offer a level of personalisation that resonates with consumers. Names, images, or intricate patterns can be etched onto the surface of plastics, creating unique and memorable products.
Finishes and Engravings:
Frosted Finishes:
Laser-engraved plastics can achieve a stunning frosted appearance. This technique is often employed to create elegant designs on acrylic surfaces, adding a touch of sophistication.
Colour Filling:
Laser-engraved designs can be enhanced by adding colour fills. This technique is particularly effective on acrylic, creating vibrant and visually appealing results.
Texture and Pattern Engraving:
Laser engraving allows for the creation of various textures and patterns on plastic surfaces. This is especially popular in the fashion industry, where unique textures can be added to accessories and garments.
The post Precision in Polymers appeared first on apt 123.
Custom Plastic Fabrication Goes Beyond Manufacturing 24 Nov 2023, 8:57 am
Custom plastic fabrication goes beyond manufacturing—it’s about shaping possibilities. From concept to creation, this process demonstrates the dynamic nature of plastics in delivering tailored solutions that meet the diverse and evolving needs of industries and individuals.
Cutting or Shaping: Depending on the design, the plastic sheets or blocks may need to be cut or shaped. This can be achieved through various methods, including sawing, laser cutting, or CNC (Computer Numerical Control) machining. CNC machines offer precision and repeatability, making them ideal for creating complex shapes and intricate details.
Material Selection: The fabrication process begins with the careful selection of the appropriate plastic material. Different plastics offer varying properties, including strength, flexibility, transparency, and chemical resistance. The choice of material depends on the desired characteristics of the final product.
Design and Planning: Once the material is selected, the next step is designing the product. This involves creating detailed plans and specifications. Computer-aided design (CAD) software is often used in this stage to create accurate and intricate designs, ensuring that the final product meets the required specifications.

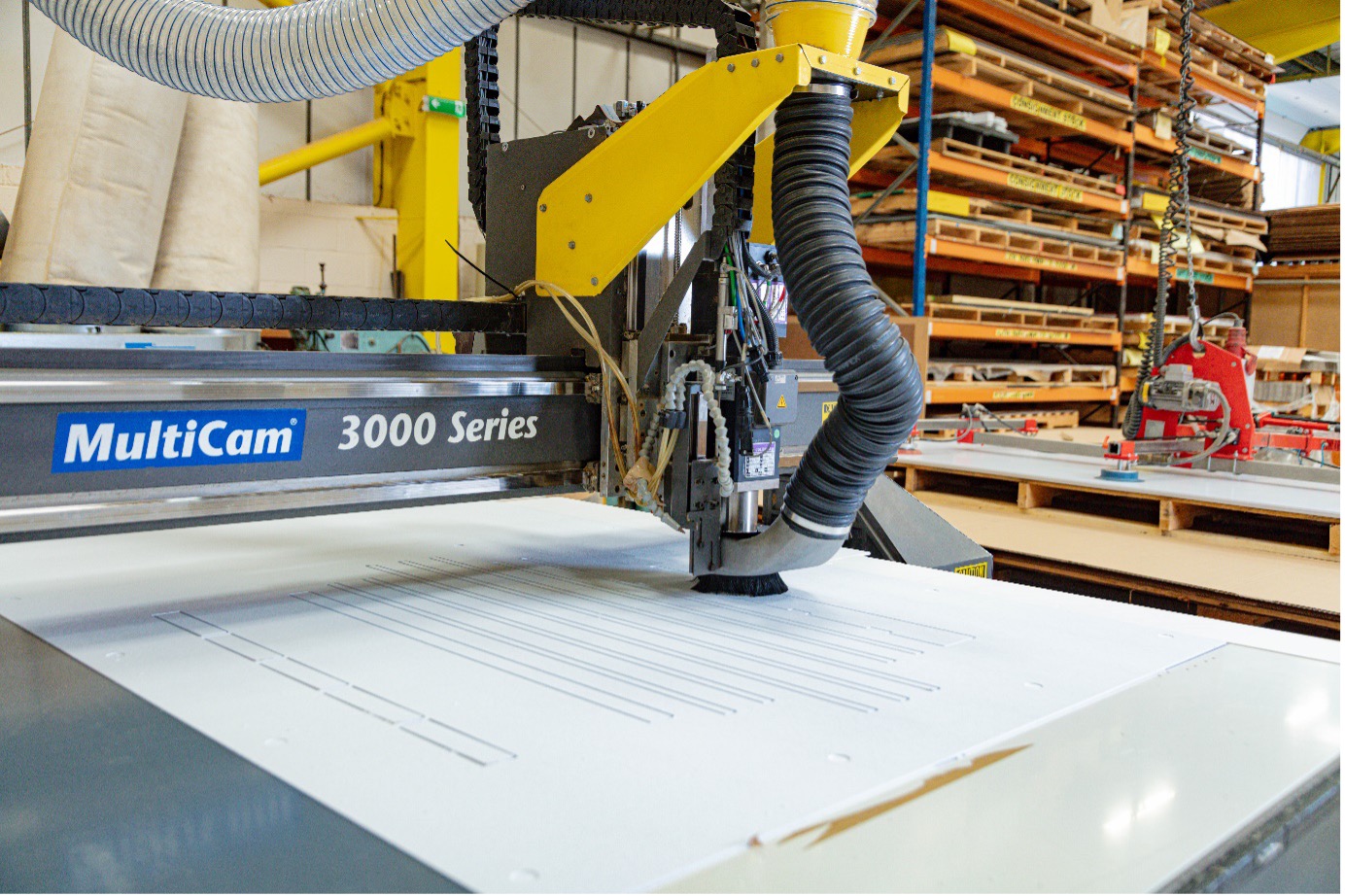
Molding: Molding is a common process in plastic fabrication. It involves shaping the plastic material by placing it into a mold and applying heat and pressure. There are different types of molding techniques, such as injection molding, compression molding, and blow molding, each suitable for specific applications and shapes.
Bending and Forming: To create curved or contoured shapes, plastic sheets may be subjected to bending or forming processes. Heat is applied to soften the material, and then it is shaped into the desired form. This method is often used in the production of signs, displays, and other three-dimensional components.
Joining: If the final product requires multiple pieces of plastic to be combined, various joining methods are employed. Common techniques include welding, adhesives, or mechanical fasteners. The choice depends on factors such as the type of plastic, the intended use, and aesthetic considerations.




Finishing: After the primary fabrication processes, the product may undergo finishing touches. This can include smoothing rough edges, polishing surfaces, or applying coatings to enhance appearance and durability. Finishing ensures that the final product meets quality standards and is ready for its intended use.
Quality Control: Throughout the fabrication process, quality control measures are implemented. This involves checking dimensions, inspecting for defects, and ensuring that the product meets the specified requirements. Quality control is essential to produce consistent and high-quality plastic products.
Assembly (if applicable): In cases where the final product comprises multiple components, an assembly stage may be necessary. This involves combining different plastic parts to create the finished product. Assembly may include additional fastening methods, such as screws or rivets.




Packaging and Shipping: Once the fabrication is complete and quality checks are passed, the final products are packaged for shipping. Proper packaging is crucial to prevent damage during transit and to ensure that the products reach the end-user in optimal condition.
These stages collectively form the plastic fabrication process, showcasing the versatility and adaptability of plastics in creating a wide range of products for various industries. The specific methods and techniques used can vary based on the complexity and requirements of the final product.
The post Custom Plastic Fabrication Goes Beyond Manufacturing appeared first on apt 123.
February’s Case Study 25 Feb 2021, 6:50 am

The post February’s Case Study appeared first on apt 123.
COVID-19 Re-usable Visors & APT “No Touch Tool” 16 Jun 2020, 7:40 am

The post COVID-19 Re-usable Visors & APT “No Touch Tool” appeared first on apt 123.
COVID-19 Safety Solutions 29 May 2020, 8:47 am
With the government having announced an easing of the lock down and outlined the back to work strategy, the responsibility now falls on all of us as employers to safeguard our staff in the workplace.
At APT we are here to help prevent the spread of Covid-19
At APT we have been supplying Clear guarding solutions for nearly 30 years, Protective screens are in high demand,
•in areas where social distancing is hard to achieve,
•on sales counters to separate employees from customers
•in offices as a division between desks
We can also make bespoke screens to your specific requirements.
All our protective screen designs are easy to assemble, Contact us on 01908 305710 or email us on: sales@apt123.co.uk to assist you with any requirements.

The post COVID-19 Safety Solutions appeared first on apt 123.
Page processed in 1.187 seconds.
Powered by SimplePie 1.3.1, Build 20121030175403. Run the SimplePie Compatibility Test. SimplePie is © 2004–2025, Ryan Parman and Geoffrey Sneddon, and licensed under the BSD License.